What Are Custom Vacuum Casting Parts and Why Are They Useful?
- hktenlita1
- Apr 16
- 5 min read
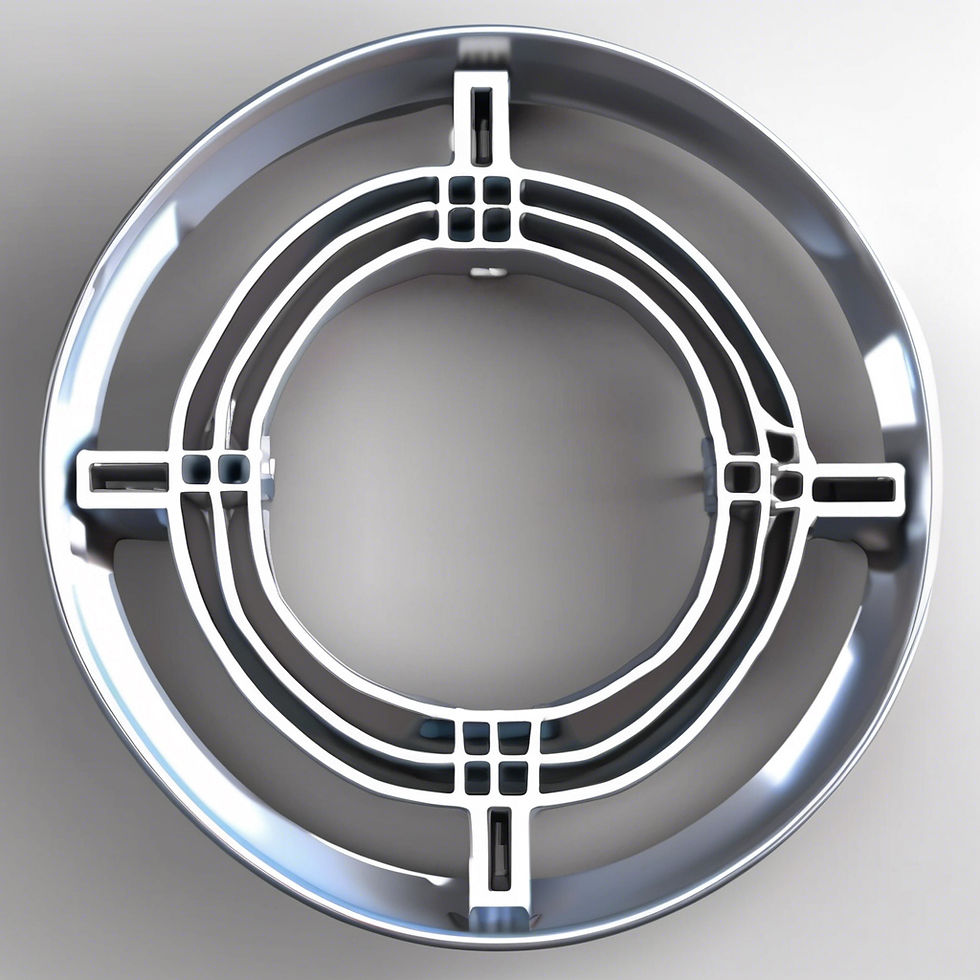
Vacuum casting is a highly versatile and cost-effective manufacturing process used primarily for producing high-quality prototypes and low-volume production parts. It involves the use of a silicone mold and a vacuum chamber to remove air bubbles and ensure accurate replication of the master pattern. Originally developed for the automotive and aerospace industries, vacuum casting has evolved to support a wide range of applications in various sectors, including medical, consumer electronics, and industrial design.
The Process of Creating Custom Vacuum Casting Parts
The vacuum casting process begins with a master model, which is typically created using 3D printing or CNC machining. This master model is used to form a silicone mold. The mold is then placed in a vacuum chamber where a liquid resin is poured and degassed to eliminate trapped air. Once cured, the mold is opened to reveal a highly detailed part that faithfully reproduces the features of the original master model. Customization can be achieved by altering the master model, selecting different resins, and incorporating colorants or additives to meet specific performance requirements.
Materials Used in Vacuum Casting for Customization
One of the most advantageous features of vacuum casting is the wide selection of polyurethane resins available. These materials can mimic the mechanical, thermal, and aesthetic properties of various engineering-grade plastics. For instance, there are resins that replicate the properties of ABS, polycarbonate, or rubber-like materials. This allows manufacturers to produce functional prototypes that closely resemble the final product, both in appearance and performance. Additionally, transparency, color, and surface finish can all be customized to suit individual project needs.
Advantages of Using Custom Vacuum Casting Parts in Prototyping
Custom vacuum casting parts offer several benefits that make them ideal for prototyping. The ability to quickly produce a small batch of high-quality parts allows designers and engineers to evaluate form, fit, and function before committing to mass production. The process is significantly faster and more economical than injection molding for limited quantities, making it an excellent choice for iterative testing. Furthermore, the high level of detail and surface finish achievable with vacuum casting makes these parts suitable for presentations, user testing, and even marketing samples.
Suitability for Low-Volume Production Runs
While prototyping is a common application, vacuum casting is also suitable for low-volume production. When producing fewer than 1000 units, the cost of creating an injection mold may be prohibitive. Vacuum casting offers a practical alternative that delivers consistent quality without the high upfront tooling investment. Custom vacuum casting parts can be used for bridge production, where products are manufactured in small quantities to fill the gap between prototype and full-scale production. This helps businesses get their products to market more quickly while still validating performance in real-world conditions.
Precision and Detail in Replication
Vacuum casting delivers exceptional precision and detail, making it ideal for applications that require tight tolerances and complex geometries. The silicone molds used in the process capture even the smallest features of the master pattern, including surface textures, undercuts, and intricate contours. This accuracy is particularly beneficial in industries such as medical device manufacturing, where part performance and compatibility are critical. The high level of detail also reduces the need for post-processing, saving both time and labor.
Versatility Across Industries
Custom vacuum casting parts are used in a wide array of industries due to their adaptability. In the automotive industry, they are used to produce dashboard components, light housings, and functional test parts. In the medical field, vacuum casting is employed to create housings for diagnostic devices, prototypes of surgical instruments, and ergonomic trial models. Consumer electronics benefit from the ability to prototype enclosures and ergonomic designs. Even in architecture and product design, the process supports the creation of aesthetically pleasing, functional models for client presentations and feasibility studies.
Supporting Product Development and Innovation
Innovation thrives in environments that encourage experimentation and iteration. Custom vacuum casting parts provide the flexibility needed to explore multiple design concepts quickly and affordably. Because the process allows for rapid changes to be implemented, designers can refine products based on user feedback or functional testing. This speeds up development cycles and enhances the final product’s quality. By lowering the barriers to prototyping and small-batch manufacturing, vacuum casting empowers businesses to innovate more freely and effectively.
Time and Cost Efficiency in Manufacturing
Compared to other manufacturing processes, vacuum casting offers a compelling balance between speed, cost, and quality. Creating a silicone mold is relatively inexpensive, especially when compared to the cost of machining metal molds for injection molding. Additionally, the turnaround time for producing a set of parts can be just a few days. This speed enables companies to accelerate their go-to-market strategy while keeping development budgets in check. For startups and small businesses in particular, this can be a critical advantage.
Enhancing the Aesthetic Appeal of Prototypes
A key benefit of custom vacuum casting parts is their visual and tactile quality. With the right finishing techniques, cast parts can closely mimic the appearance of injection-molded products. They can be painted, textured, polished, or even coated with special finishes to match the intended final product. This makes them ideal for high-fidelity prototypes used in investor pitches, trade shows, and focus group testing. The ability to convey a realistic vision of the product enhances credibility and market acceptance.
Streamlining Design Validation and Testing
Design validation is a critical phase in product development. Custom vacuum casting parts help streamline this process by offering functional prototypes that closely match the final product’s performance. Engineers can subject these parts to mechanical stress, thermal cycling, and other tests to ensure durability and compliance with specifications. Feedback from these tests can be used to optimize the design before scaling up production, reducing the risk of costly mistakes or recalls.
Bridging the Gap Between Concept and Production
Many companies face a challenging gap between the concept stage and full production. Custom vacuum casting parts provide an effective bridge by enabling functional testing and market sampling without committing to large production volumes. This is particularly useful in industries with rapidly changing consumer preferences or short product lifecycles. It allows businesses to launch products with confidence, knowing they’ve been validated through comprehensive testing and real-world evaluation.
Customization and Personalization Options
Customization is a growing trend across various industries, and vacuum casting supports this demand effectively. Whether it’s creating medical devices tailored to individual patients or consumer products in bespoke colors and textures, the process allows for extensive personalization. Since molds are made quickly and inexpensively, it’s easy to create multiple variants of a product without incurring significant additional costs. This level of flexibility supports niche markets and high-value applications where customization is key.
Environmental and Sustainability Considerations
While vacuum casting uses synthetic materials, the process itself can be more environmentally friendly compared to traditional manufacturing methods. Because it is ideal for small runs and prototyping, it reduces material waste and energy usage associated with mass production. Additionally, the reusability of silicone molds for multiple parts contributes to resource efficiency. As sustainable manufacturing becomes increasingly important, vacuum casting provides an option that aligns with eco-conscious development practices.
Leveraging Expertise from Specialized Manufacturers
Working with a manufacturer that specializes in custom vacuum casting parts offers additional advantages. These experts can provide guidance on material selection, design optimization, and process improvement. They also ensure consistent quality and performance across multiple production cycles. By leveraging their experience and capabilities, companies can maximize the benefits of vacuum casting and integrate it more effectively into their development workflow.
Conclusion
Custom vacuum casting parts have become a cornerstone of modern prototyping and low-volume production. Their ability to deliver high-quality, detailed, and functional parts quickly and affordably makes them indispensable in today’s competitive manufacturing landscape. Whether you’re developing a new product, testing a concept, or exploring customization options, vacuum casting offers a flexible and reliable solution. As industries continue to prioritize speed, innovation, and sustainability, the value of custom vacuum casting parts is only set to increase.
Comentarios